Related documents
Related links
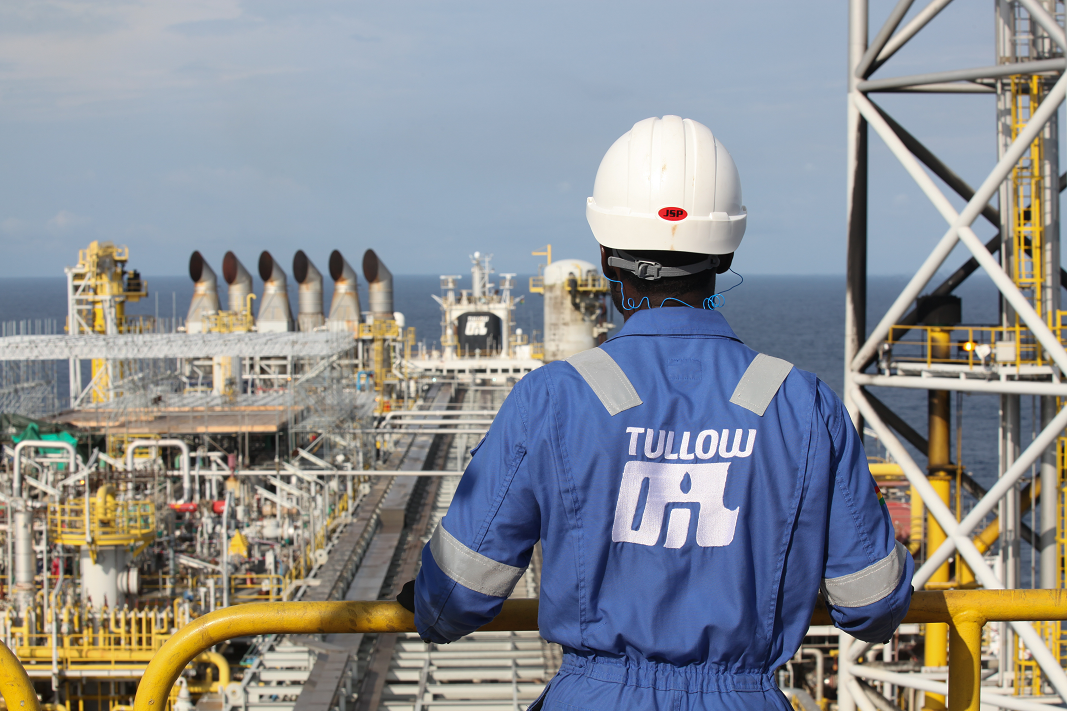
Tullow is committed to the highest standards of health and safety and we strive every day to maintain a positive safety culture across our business. We have a culture of working hand in hand with our contractors as one team, working to keep everyone safe and healthy.
We adhere to all laws and regulations governing safe working and, in many cases, our internal standards go above the requirements of the law. We continue to monitor key health risks related to our operations and take preventive action where possible. A known risk, for example, is malaria and we recorded no cases among staff and contractors that have no immunity to Malaria in 2020. Managing Tullow’s response to the COVID-19 pandemic dominated much of the year. Thorough risk assessments and plans were put in place across our operations, both on the FPSOs and in the office to protect the health of our staff and contractors, whilst maintaining safe COVID-19-free production operations and work environments.
Tullow’s safety performance in 2020 for lost time injury rate (LTIR) and Total recordable injury rate (TRIR) indicate that we injured more people in our operations compared to 2019. Fortunately, none of the events were life changing, but never-the-less, we strive to eliminate injuring people associated with our operations. Notable occupational safety achievements in 2020 included zero total recordable injuries at our Ghana offshore TEN and Jubilee floating production storage and offloading facilities (FPSOs) and zero total recordable injuries in our Kenya facilities. Despite these positive aspects of our safety performance, during 2020, we experienced a similar number of high potential incidents (HiPos) compared to 2019. Although we work to avoid HiPos, transparent reporting of them is vitally important and actively supported at Tullow, so that we can continually learn and make improvements. Following a number of HiPo events associated with our Tullow Ghana operations, the Tullow Ghana leadership held a series of safety stand-downs across all parts of the business.
In 2020 we spent time analysing similar or repeated incidents that have occurred over the years at our Ghana operations. These reviews have informed where our assurance activities are to be focused and are leading to improvements to our incident investigation processes. Part of these improvements included the company wide implementation of a new incident reporting, investigation and action tracking software tool.
“Tullow's 2020 IOGP lifesaving rule awareness campaign was the most inspiring and engaging I’ve ever participated in and I am confident will translate to a better safety performance in 2021.” - Rowland Wright, Environment, Health, Safety and Asset Protection Manager, Tullow Ghana
The highlight of 2020 was Tullow Ghana’s IOGP lifesaving rule awareness raising campaign. We spent a significant effort launching the IOGP life saving rules, which supplemented our existing procedures with a set of industry wide and strictly enforced rules aimed to reducing the likelihood of fatal incidents. The rules provide lifesaving actions over which an individual has control at the worksite, to protect themselves and colleagues from injury and fatality. The awareness campaign spanned a three month period, involved senior leadership and all contractors involved in our operations, promoting each rule and involved presentations, experience sharing, quizzes and more.
In 2021 we have embarked on a one year campaign to promote the IOGP process safety fundamentals (PSFs), to significantly enhance the understanding of process safety and engage our workforce in relation to how our actions play a vital role in preventing process safety events from happening. Process safety events can have catastrophic outcomes with multiple fatalities. There causes are often complex, with many barriers failing to prevent the event. The PSFs are a set of basic principles for front-line workers, supervisors, and managers that emphasise existing good practices to prevent fatalities from process safety events. It is intended that the adoption of fundamentals will provide focus for process safety on the front line, enable process safety concerns to be raised more readily and move towards an industry wide language for process safety.